CESENA, ITALY – An immense company with a total of 21,240 square metres, 10,800 square metres of warehouse space and the same amount given for office space, where (almost) nothing is manufactured. It seems counterintuitive, yet for REPA in Cesena this is imperative for dealing with their logistics, an added service to make spare parts move around the world. This is also possible thanks to computers dedicated to spare parts, where seven million worth of data are saved to guarantee a targeted, always precise and quick service.
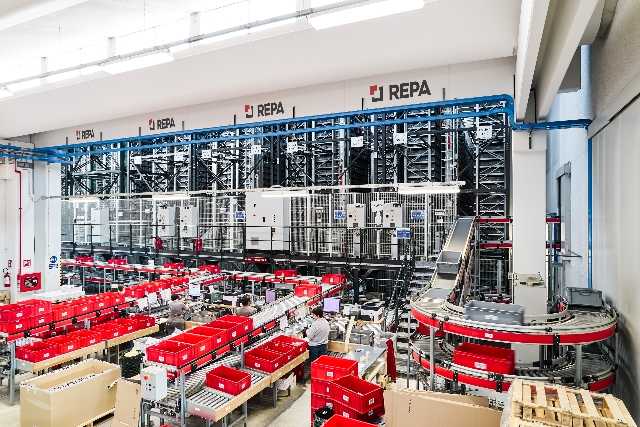
Yes, because this is a different facility from the others. The core business of REPA Italia, the Italian branch of the American Parts Town Unlimited, is the handling and distribution of spare parts. With 60% of shipments in Italy, 40% worldwide and technical customer care in twenty languages. With a dedicated service for finding parts, ready and available if the customer cannot find them on their own on the company website.
There is always a lot of work for REPA, because all the equipment, such as espresso machines, which combine water and heat, are bound to eventually wear out. And broken parts must be replaced, as quickly as possible. This is REPA’s specialty.
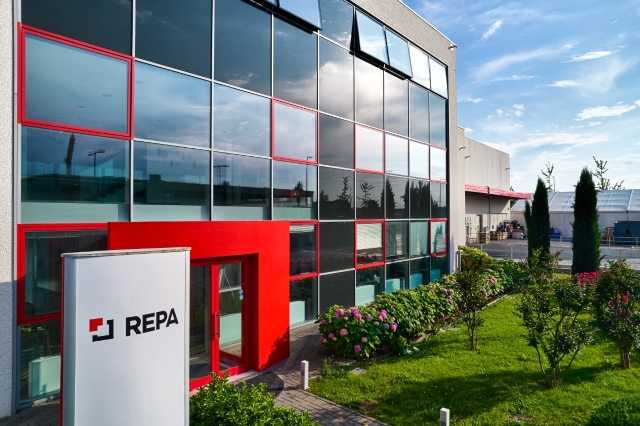
REPA is the root of the Latin verb “reparare” and is understood in all languages
But let’s start from the beginning, more precisely why this City of Spare Parts is called REPA. The company name is the result of an employee contest in which REPA came out on top being the root of the Latin verb “reparare” and is used in all languages. Starting with English “repair”, “reparar” in Spanish and Portuguese or “reparieren” in German, but also “réparer” in French.
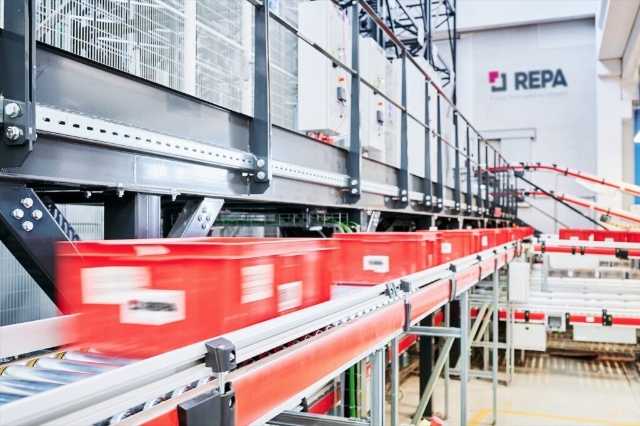
A few dates to complete the history of the REPA Italia brand which, in 1982, was founded in Cesena with the name LF. Then, in 2018, five leading parts distributors in Europe formed a group consisting of LF (Italy), GEV (Germany), EPGC (France), ATEL (Italy) and CCS (UK). Furthermore, in 2019, REPA The Spare Parts Group was founded, an umbrella brand, uniting the five European companies.
The name changes
Finally, in 2022, the REPA group was acquired by the US Parts Town Unlimited, already owner of First Choice (UK). In March 2023, following a rebranding activity, LF was renamed REPA Italia, GEV became REPA Deutschland, EPGC was renamed REPA France, GEV Recambios became REPA Iberia, while CCS together with First Choice were renamed Parts Town UK. ATEL of Udine, specialised in the distribution of vending spare parts, kept its name.
The six company values
There is one aspect in Cesena that makes everyone very proud and which is always emphasised during the presentation of the visit: the six company values. They are challenging, but practiced in REPA every day: safety, integrity, community, passion, courage, innovation. Which is to say that the City of Spare Parts always puts its heart and soul into everything it does.
Today, REPA also means 200,000 items in the REPA Italia warehouse with over 2,000 brands in their catalogue, of which 50 from manufacturers of coffee machines, coffee-grinders dosers. For some, such as Rancilio, Simonelli Group, Astoria and Wega, REPA boasts a distribution agreement for original spare parts to support the growth of the partner and the brand.
REPA opens its doors to all OEMs (acronym for Original Equipment Manufacturers) who believe in REPA’s value proposition is to support their customers in terms of service, original spare parts and logistics solution.
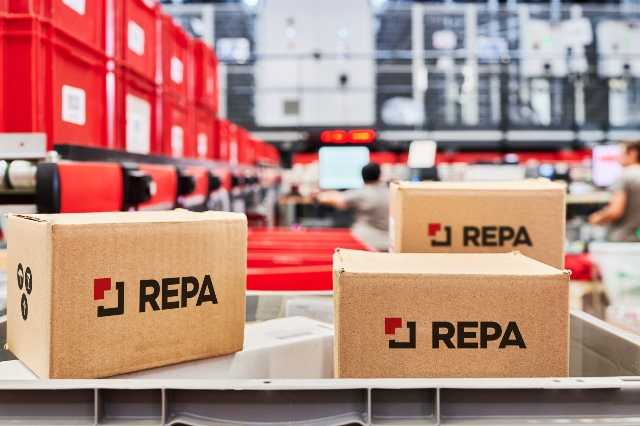
REPA collaborates with the best OEMs on the market
These manufacturers entrust it with the management and distribution of their spare parts, entering into partnership agreements and also obtaining visibility on the REPA company website and at the main industry exhibitions fairs around the world where the Cesena company is always exhibiting with on a dedicated branded stand with the REPA team in attendance.
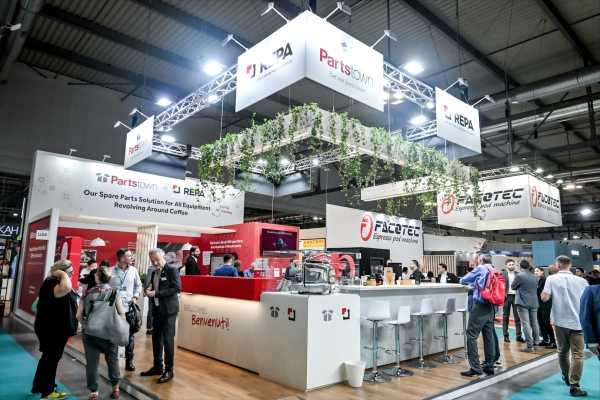
Many OEMs have long chosen REPA for the high level of technical assistance offered to its customers. This is obtained thanks to the widespread presence in the territory, the numerous logistics centres, the strong expertise in the spare parts business. This allows REPA to offer partners the best solutions for effectively managing their equipment repair parts. And perfect after-sales customer support.
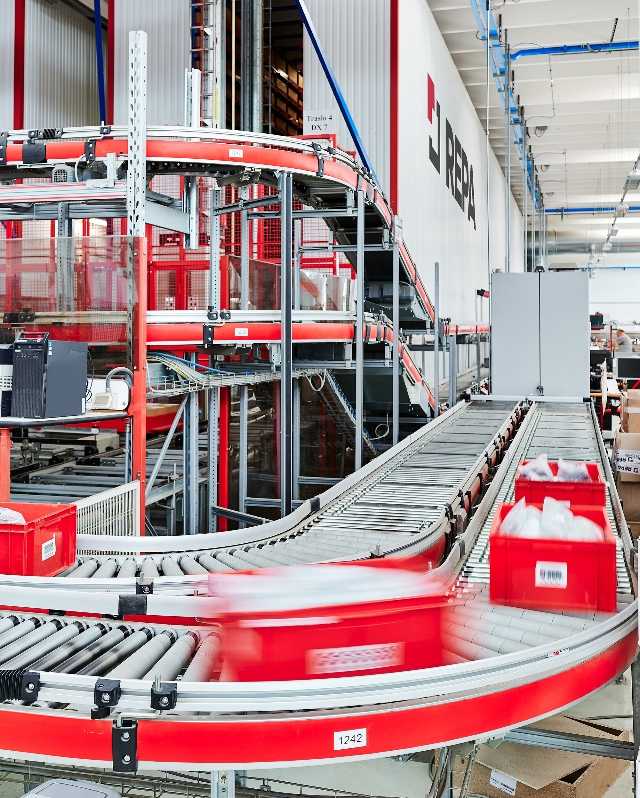
When you arrive at REPA Italia, you immediately look for where the cardboard boxes are prepared. Those with the different pieces to be sent all over the world, also thanks to the synergies with the REPA network. Everything happens almost in real time, with same-day shipping for orders arriving before 4pm, next-day delivery in Europe and 4-5 days later worldwide.
Almost in real time, true, but only for in-stock orders. For some processes, in order to be shipped, spare parts must first arrive and be catalogued in the warehouses.
The REPA Italia headquarters in Cesena is divided into four sectors, all immense: cathedrals of spare parts.
In the first one, hundreds of containers of parts arrive from the respective manufacturers. Behind it is the gasket packaging area. Then a huge vertical warehouse with 72,000 items readily available. And the spectacular automatic handling, with robots that move at dizzying speed vertically and horizontally.
Finally, the department that everyone thinks of when talking about REPA and original spare parts: preparing packages. But, in the same sector, there is also the more demanding packaging of pallets and even 20-foot container. The latter are usually shipped to the most distant customers.
To manage all these processes, the Cesena plant is always operational 16 hours a day. Therefore, from 6am to 10pm, with different shifts of employees taking turns at the many workstations.
It all starts with the arrival and unloading of goods
The four dedicated loading bay doors feature the typical high speed vertical shutters also found in Formula 1 pits. The Imola Circuit is nearby, they must have been inspired by it. An indicator, if there were still any doubts, that here everything happens quickly. Behind quality control is the gasket packing area.
Incoming goods arrive immediately at quality control. A key location in the factory. At these 18 stations that check that each piece corresponds to the one requested and is not damaged, a stream of spare parts arrive. At least a thousand are sorted every day, over 5,000 every week. REPA‘s constant aim is to have items in stock within two days of arrival.
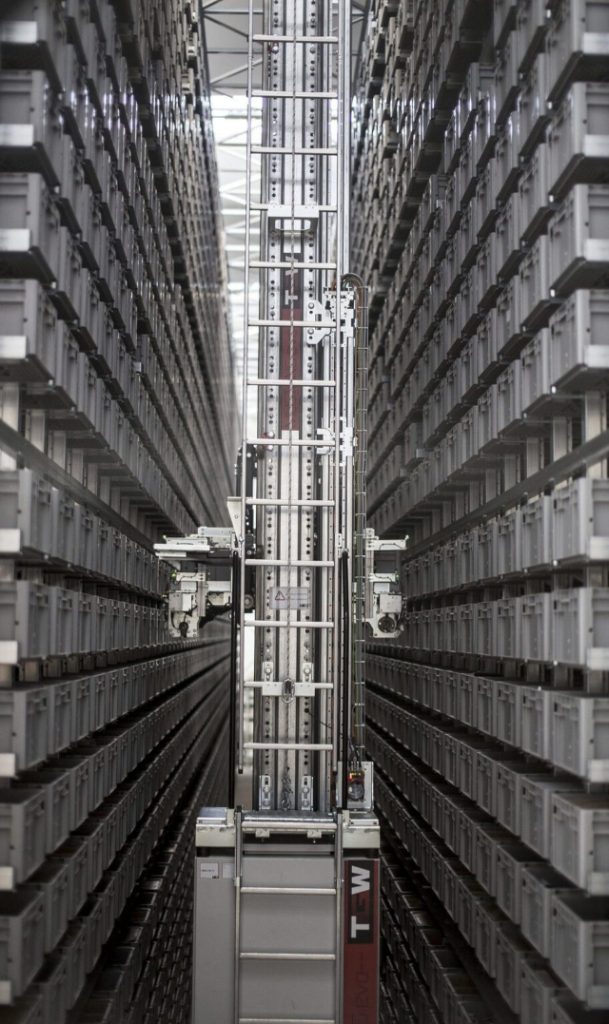
Then everything, original spare parts and gaskets, is placed in what REPA defines as “department stores”. However, these spaces do not resemble a large shopping centre. They rather look more like medieval castles with surrounding walls and 10 metre high towers, like a three-story house.
Inside the warehouse drawers, there are 72,000 different pieces. REPA computers have the task of knowing where every single spare part is located in order to send the robots to collect them. Seen up close, it all seems quick and easy. But at the base there is a very complicated software with seven million worth of data and a run-in that we imagine will not be easy.
There are three department stores, the beating heart of REPA
The fully automated one, for piece loading and picking, has seven lanes, six picking stations, 50,000 boxes with a continuous cycle sequential picking system. 65% of the spare parts in stock can be found here.
17% of the stock is found in the Cranes Static Location stackers. Here there are four lanes, as many collection stations and 6,500 boxes.
The third warehouse is the Narrow aisle warehouse. The remaining 18% of the goods are found here. In particular the large ones, which do not fit into the boxes, and the chemical products also for cleaning the machines. The pieces are picked via pallet trucks and motorised order pickers which move the pieces arranged in 5,500 pallet spaces.
Everything takes place automatically, always with double and cross checks through the bar codes applied to the pieces.
This starts from the entrance to the internal route, to quality control, in order to avoid errors in the pieces to be shipped.
REPA Italy is extremely strict on this. Because in Cesena they know well that selling, shipping, a piece other than the one needed and requested is not only a nuisance for buyers. Yes, because it is also a disaster, as the damaged equipment remains broken until the next shipment.
This causes a waste of time and inevitable tensions with customers. The reality is that today in REPA, errors, even with around 200,000 parcels leaving, are reduced to 0.08%. A percentage so low that the customer who stumbles upon it could even bet on the shipment number at the local lottery.
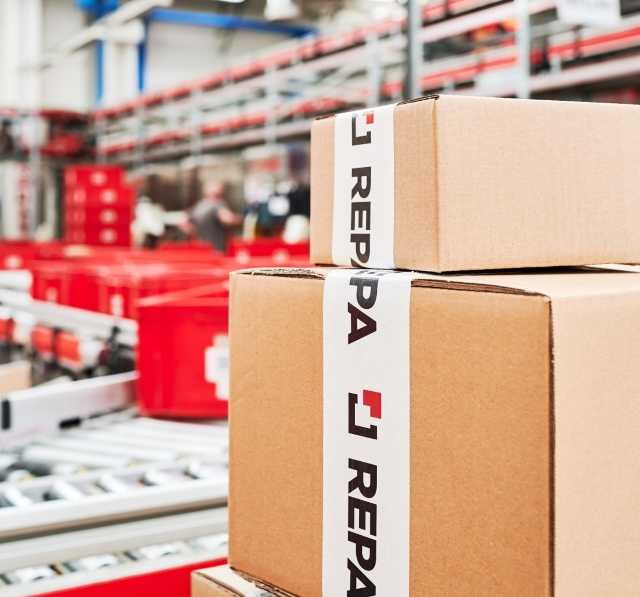
At packaging, where the parts arrive through automatic conveyors, the spare parts end up first in a consolidation line and then in another five destination lines. Here, small parcels, medium ones and multi pallets are prepared.
REPA underlines that the further from the warehouse the customer is, the larger the container. This is due to transportation and on-site assortment costs.
The shipping department
Shipments coincide with the pace of incoming sorted items. A thousand containers are emptied upon arrival, behind the shutters of Formula 1; there are approximately one thousand shipments per day, of which 150 are large parcels, on pallets. For a few years, every 31st December, the counter has reached 200,000 parcels delivered to couriers. The weights of the packages? They range from 1 to 1,000 kilograms. During the visit, we followed the simultaneous preparation of many boxes, 11 pallets and a 20 foot container.
The sealing of the parcels, in a special department next to the packaging department, coincides with the application of the consignment note for the courier. Before sealing with straps and plastic film, yet another check, certified by computers, on the contents of the box or pallet.
Separated, detached from the main flow, there is the special sector that supervises the preparation and packaging of compressors for commercial refrigeration. Then, the complete kits are prepared for each appliance and the multiple packaging of fragile items.
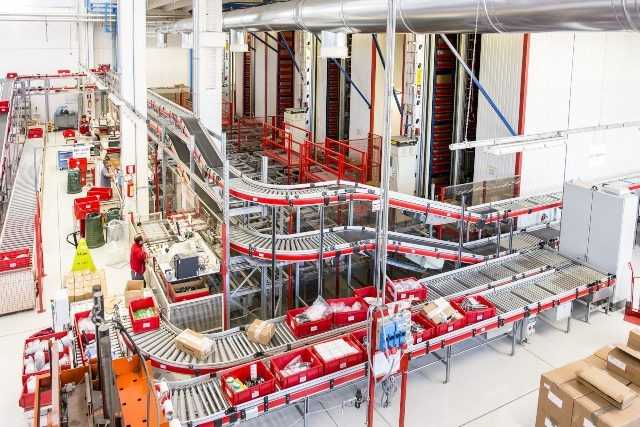
Finally, the loading of goods with European and global fast couriers
All the main European and global carriers have a branch in Cesena and every afternoon they show up in sequence at the cargo loading gates. The agreement between REPA and couriers provides for delivery within 24 hours throughout Europe. Even the next day, if the order arrives at the Cesena office by 4pm.
But in this huge company that provides an added service on spare parts, timely deliveries and certainty that the order coincides with dispatch, there are also other strengths. Always in the name of customer service, always for B2B.
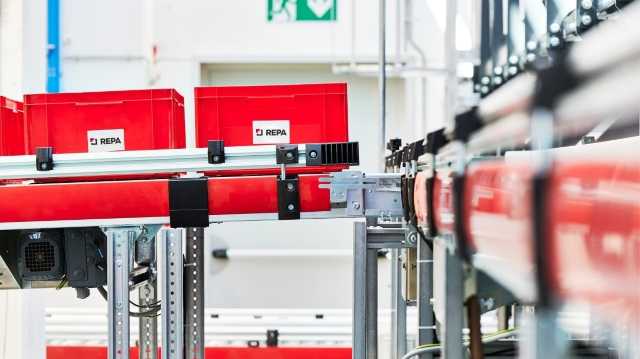
And this further strength is called customer assistance, yet another flagship for REPA. Because, if the company website has become the first seller, as explained in Cesena, human support is never lacking. This is if the part the customer needs cannot be found through the site.
Therefore, they took us to visit a large office dedicated to customer care, where the operators are all specialised technicians who speak 20 languages. The goal is to provide cutting-edge service to customers in need. A service that works both via telephone and e-mail.
This is the World of Beans, as they call it in REPA
The world that revolves around the coffee bean. World of beans, as we saw in Cesena, means simplifying the activities of all the actors involved in the coffee supply chain. Therefore, importers of machines, roasters, service centres etc.
In this sense, REPA presents itself as a simple and, at the same time, global solution provider to allow all coffee equipment to always be kept functioning. And not only that. With REPA, coffee customers can benefit from all spare parts from a single supplier, one-stop-shop.
Easy to find, immediately in stock, delivered every day worldwide. And all this, in Cesena, can be experienced first-hand.
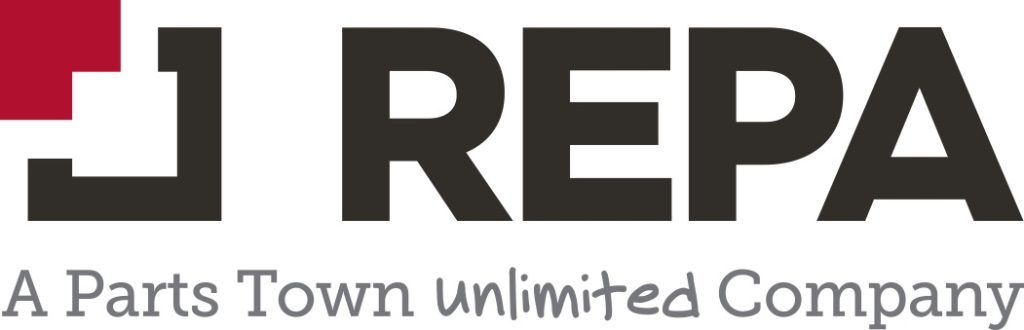
About REPA
REPA is the leading European spare parts distributor for foodservice equipment, coffee, vending machines and household appliances and is a trusted partner to equipment manufacturers. Since 2022 REPA is a division of Parts Town Unlimited, the global leader in high-tech distribution of mission-critical equipment replacement parts, related products and services for the foodservice, residential appliance and HVAC industries.
REPA customers benefit from strong expertise in spare parts, with more than 40 years of experience in the market from REPA Italia, REPA Deutschland, REPA Iberia, REPA France, ATEL and Big Warehouse.
With the industry’s largest inventory accessible through state-of-the-art webshops, high stock availability, highly innovative logistic centers that assure the fastest delivery of spare parts in the industry, REPA provides every customer with the right part, at the right time, everywhere.
For more info click here.
The REPA Group in numbers
Number of employees: over 1,000
Technical support in over 20 languages
Over 50,000 customers in 44 European countries and in 188 countries around the world
Distribution centres in 7 countries: Italy, Germany, France, Spain, UK, China, Australia
Number of annual shipments: over 1 million
Database articles: approximately 7 million
Items in stock: 200,000
Brands: over 2,000 (of which 50 coffee)
Sectors: Spare parts for HoReCa, Refrigeration, Coffee, Vending, Domestic
REPA Italia in numbers
Number of employees: 267 (163 in the office, 104 in the warehouse)
Total surface area (exterior, offices, warehouse): 21,240 square metres
Warehouse surface: 10,800 square metres
Number of stacker cranes (automated warehouses): 11
Items in stock: 72,000
Daily parcels: over 800
Average number of parcels per year: approximately 190,000
About Parts Town Unlimited
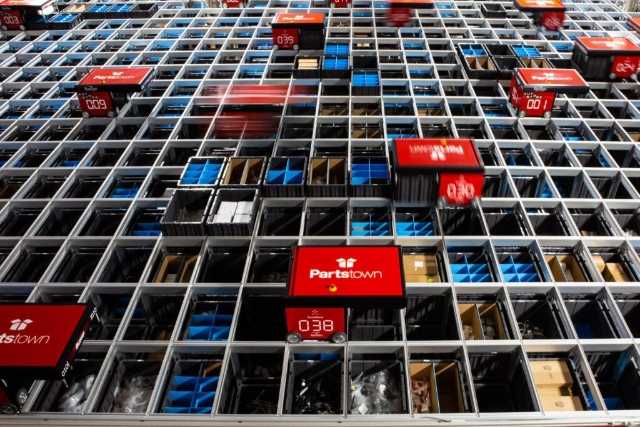
Parts Town is the leading, technology innovation-driven distributor of genuine OEM (original equipment manufacturer) foodservice, residential appliance and HVAC equipment repair parts. When there’s a hiccup with any piece of equipment, Parts Town is ready to jump in and help with the most in-stock parts on the planet, innovative technology and an unmatched customer experience. Customized solutions benefit equipment service technicians of all kinds, as well as chain and independent restaurants, schools, health care facilities and hospitality providers.
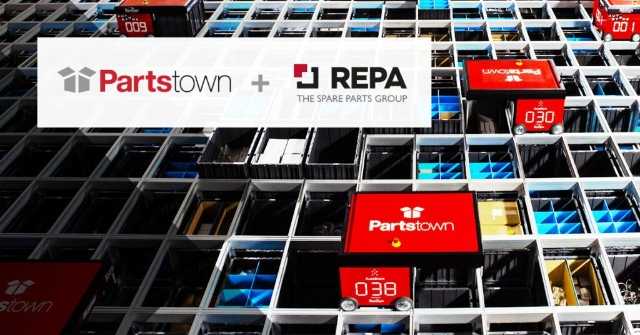
By partnering with the top manufacturers of foodservice, residential appliance and HVAC replacement parts, Parts Town improves the supply chain, increases sales of genuine OEM parts and keeps every customer’s business running like clockwork. Parts Town also partners with equipment and supplies dealers of all sizes to offer a one-stop-shop through its Parts Town marketplace.
For more info click here.